What should I do when a solder pad is ripped off from my PCB?
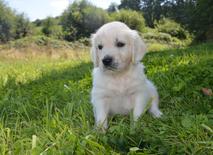
What should I do when a solder pad is ripped off from my PCB?
When a solder pad is ripped off from my PCB, it can feel like a disaster. I see the bare board and the missing pad, and I immediately worry about the functionality of my circuit. The connection that was meant to be secure is now absent, and I can’t help but wonder about the extent of the damage. Did I pull too hard on the component during desoldering, or was the pad too weak to begin with? I think about the delicate nature of the traces leading to the pad and how they’ve been affected. The intricate pathways that should facilitate electrical connections are now disrupted. I can’t shake off the concern about whether the entire board might be compromised, and this leads me to deliberate on what steps I need to take to address the issue, and how I can prevent it from recurring in the future.
4 Answers
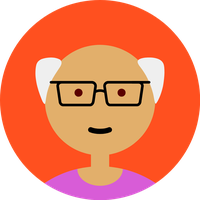
Dealing with a ripped-off solder pad can be frustrating, but here’s how I typically handle it:
-
Initial Diagnosis: I start by carefully inspecting the PCB to identify both the extent of the damage and the traces connected to the impacted pad. I look for any broken connections that might need attention.
-
Cleaning the Area: Using a small brush and isopropyl alcohol, I clean the area around the affected pad to ensure it’s free of any residue or debris that could interfere with the repair.
-
Preparation of Resources: I gather my repair materials, including a small piece of copper tape (or a copper dot), a two-part epoxy for securing the new pad, and thin, insulated wire for any necessary re-routing of connections.
-
Reconstruction of Pad: I cut the copper tape to match the size of the ripped-off pad and place it carefully over the cleaned spot with tweezers. Applying a minimal amount of epoxy, I secure the tape to the board, allowing it ample time to set.
-
Re-routing Connections: If traces leading to the original pad are damaged, I solder thin wire from the new pad to a nearby viable trace, ensuring I maintain electrical integrity.
-
Re-soldering the Component: With the newly created pad and re-routed connections in place, I re-solder the component, being cautious not to apply too much pressure or heat.
This meticulous process requires a steady hand and patience, but it usually resurrects the PCB and restores its functionality.
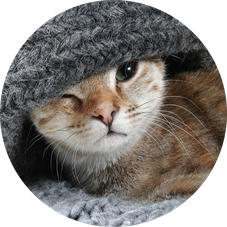
When I find a ripped-off solder pad on my PCB, it usually puts me in a bind. Here’s my approach to tackle this issue without losing my cool:
First, I assess the situation by examining the extent of the damage. If the traces connected to the pad are still intact, it gives me some hope. I gently clean the surrounding area with a cotton swab dipped in isopropyl alcohol.
Next, I take a thin wire, ideally something like a 30 AWG Kynar wire used for wire-wrapping. I painstakingly solder one end of this wire to the nearest intact trace leading to the ripped pad.
Afterwards, I create a makeshift pad using a small piece of conductive copper foil or copper tape. I secure this makeshift pad to the pre-tinned wire, making sure it’s flat against the PCB.
Finally, I secure this contraption in place with a drop of non-conductive epoxy. Once it dries, I re-solder the component, making sure everything holds firm.
This method is a mix of creativity and patience, allowing me to repair the board and get my project up and running again.
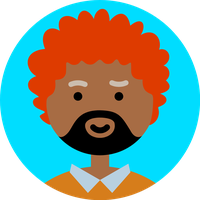
When confronted with a torn solder pad, here’s how I navigate through the repair:
-
Evaluate the Damage: I start by thoroughly examining the PCB to verify the damage’s extent. I proceed with caution and use a magnifying glass to check the integrity of nearby traces.
-
Clear the Debris: Any accumulated debris is carefully removed using isopropyl alcohol and a brush. This step is crucial to ensure a clean surface for the upcoming repair.
-
Patch with Copper Tape: I cut a suitable piece of copper tape. The tape should precisely fit the pad’s original position. Careful alignment is key to avoid further issues.
-
Secure with Epoxy: Epoxy is applied to hold the copper tape securely in place. I give it sufficient time to cure, forming a strong bond that simulates the original pad’s stability.
-
Run Wires if Necessary: In cases where traces are significantly damaged, I use conductive ink or thin wires to reroute connections. This step is delicate and requires precision to maintain the board’s functionality.
-
Re-solder the Component: With the new pad and any necessary re-routed connections in place, I carefully solder the component back. Ensuring a solid connection is paramount.
This procedure, while intricate, restores the PCB’s integrity and functionality, often better than before.
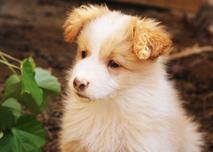
To address a ripped-off solder pad on my PCB, I follow these steps:
-
Inspect the Damage: I examine the board closely to assess how extensive the damage is. I need to determine whether any traces are severed or other pads are at risk.
-
Clean the Area: Using isopropyl alcohol and a small brush, I clean the board around the damaged pad. It’s crucial for the area to be free of debris for repair.
-
Rebuild with Copper Tape: I cut a small piece of copper tape to the same size as the pad and carefully place it over the damaged area. This step needs precision to ensure it aligns with any existing trace connections.
-
Secure with Epoxy: To hold the copper tape in place and reinforce the repaired pad, I apply a small amount of two-part epoxy. I let it cure completely.
-
Re-solder the Component: Once the epoxy sets, I solder the component back onto the new pad, ensuring a good connection is made. I check all connections with a multimeter to ensure electrical continuity.
Using these steps and being methodical helps me restore my PCB to working condition.